Leak testing is essential in the aerospace industry to ensure the safety and reliability of aircraft. Here are some of the leak testing solutions commonly used in this field:
1. Altitude simulation tests: in our chambers, we can simulate the behaviour of parts or packaging as they rise to altitude. It should be borne in mind that in the hold of an aircraft, a negative pressure of between -250 and -300 mbar is applied.
2. Air transport simulation: long-haul flights can last several hours, during which time parts may be subjected to significant negative pressure. We can simulate these high-altitude conditions in our chambers.
3. Testing in extreme conditions: we can also simulate the vacuum that exists in space in a vacuum chamber. This vacuum, which is close to absolute zero, can be simulated in specific housings that are designed and fitted with connectors adapted to withstand these extreme conditions. In these chambers, we reach vacuum levels close to 1 to 5 mbar residual. Approximately -995 mbar relative.
4. Bubble test: this method involves applying a vacuum to a hermetically sealed part that has been immersed. If bubbles appear, they indicate a leak, and locating the leak is made easier by the presence of bubbles at the site of the leak.
5. Tracer gas tests: tracer gases are injected into the system and their presence is detected outside the system using sensitive sensors. This method is used to pinpoint leaks, even in complex components.
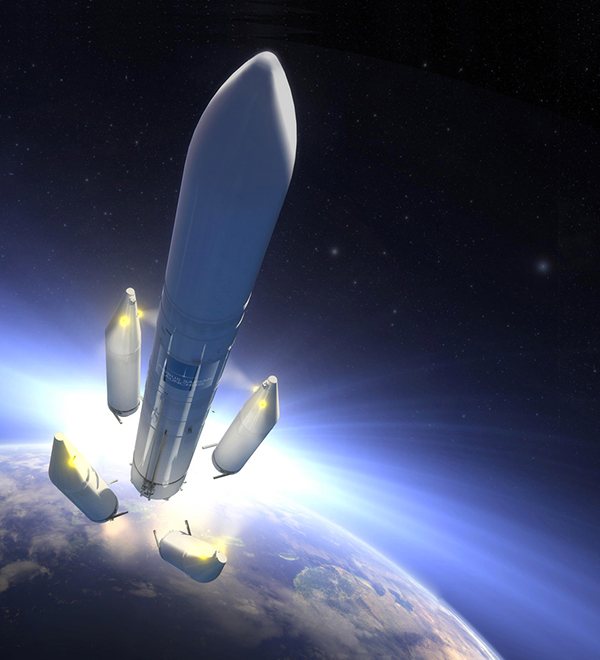
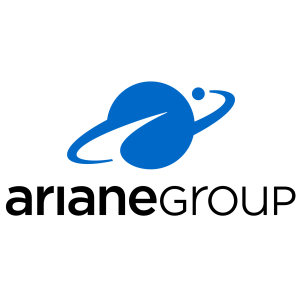

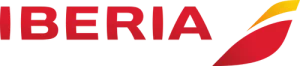
Some of our customers…
These different leak testing solutions are often used in a complementary way to ensure reliable leak detection in aircraft and aeronautical components. We regularly work with industry players to improve the performance of their products, as well as our own.
In the vacuum chamber, we will vary the pressure to simulate these conditions.
For example, if we simulate an altitude between 0 and 12,000 m, the vacuum in the chamber will go from 0 to -820 mbar relative (192 mbar absolute).
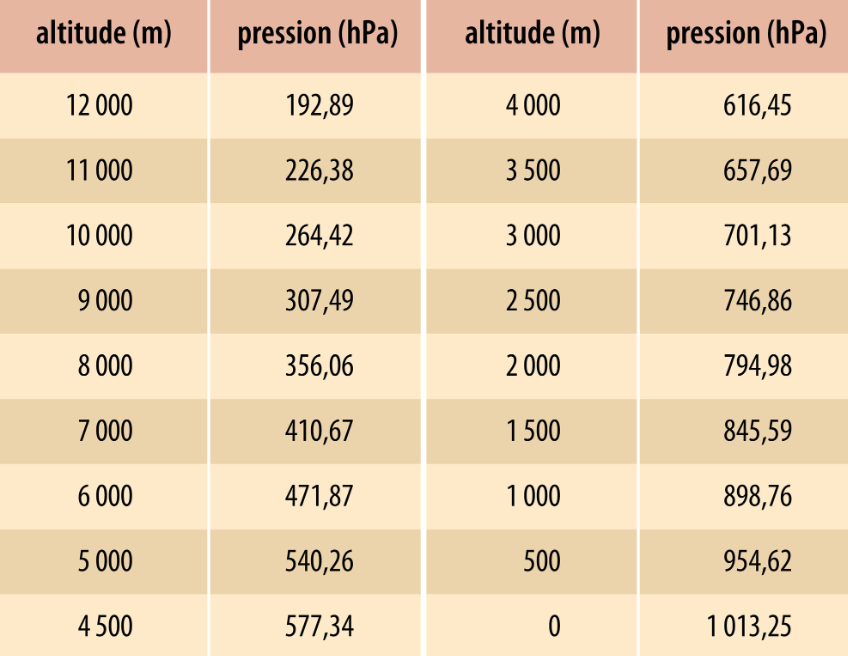