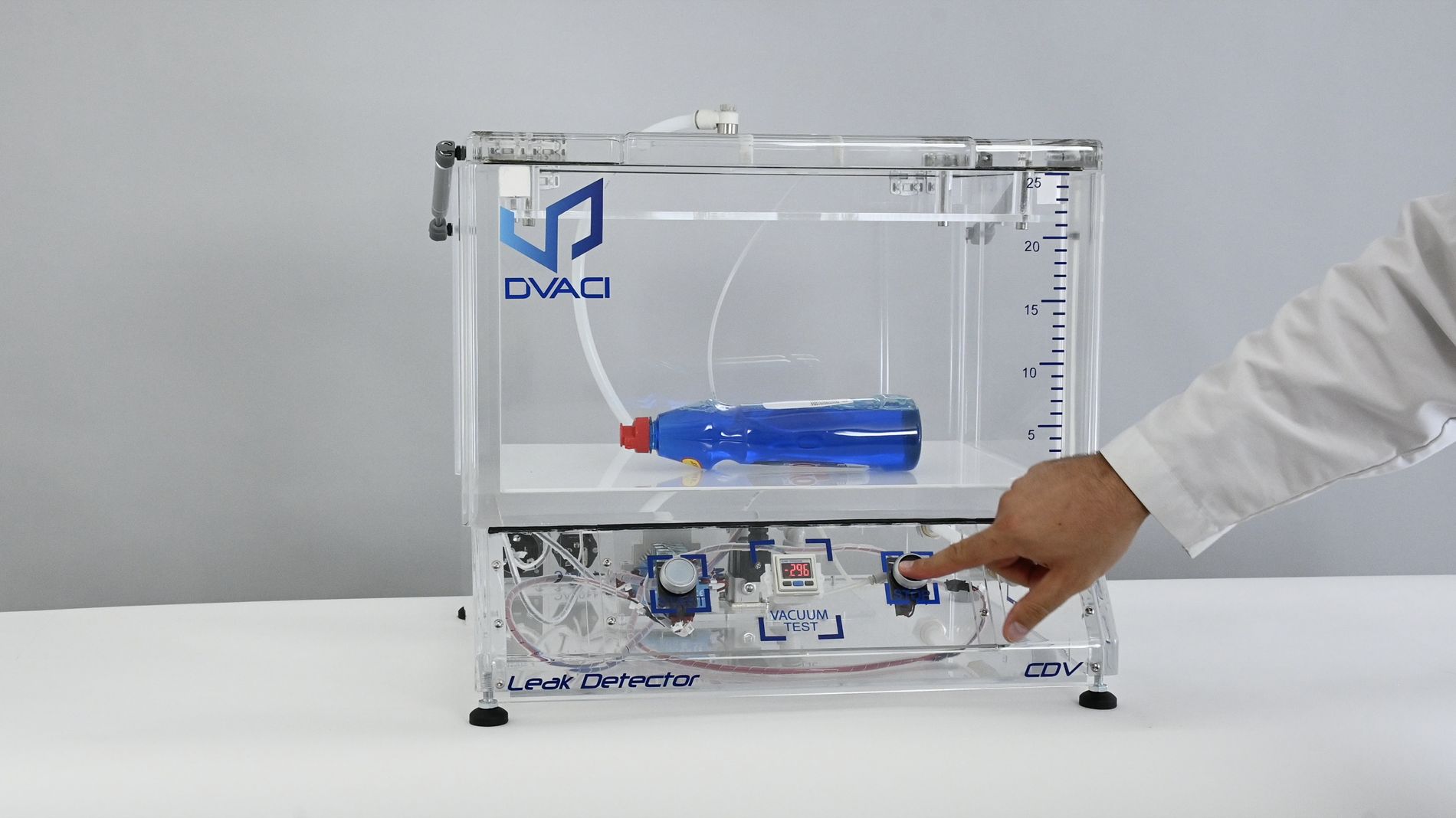
There are a number of different methods, and we’re going to take a look here at the methods we offer our customers that can be used in our equipment.
Destructive testing
These are the classic tests which can be carried out on the production line itself or in a quality control laboratory.
The first test is called the “bubble test” or the bubble visualisation method.
Leak test in vacuum chamber with visual bubble detection
Case of packaging containing solids or powders and still containing air or a modified atmosphere (M.A.P.)
This is the most common test and the easiest to perform. All you have to do is fill the chamber with water or a liquid containing a dye. Once the chamber is full, the samples to be tested are immersed in the chamber and the lid is closed to keep them submerged.
Once the samples are in place, the pressure in the residual air in the chamber is reduced. This pressure difference between the inside and outside of the packaging means that the air contained inside the packaging will tend to want to come out to balance the pressure between the inside and outside.
So if there’s a defect on the packaging, air bubbles will escape from the defect and the leak will be visible with a bubble emission.
You can see how it works in the video below
Flexible or rigid packaging containing liquids
In this case, the sample pack is placed in the chamber so that the area likely to leak is in contact with the liquid contained in the pack. So for well-filled bottles we put them in a horizontal position and for slightly less well-filled bottles we put them upside down.
Once the pack is in position, we create a vacuum around the pack, so that any residual air inside the pack is trapped, forcing the liquid contained in the pack to try and find a way out. This exit is usually a leak or a leak in the seal. In this way, you can visually see the liquid flowing out of the packaging.
Empty packaging containing no residual air
The two previous methods work well because there is still air inside the packaging and this air plays an important role in the test method.
If we are dealing with a vacuum pack, our teams have developed a method for injecting air into the pack to simulate a pressure difference with the outside of the pack and thus visualise bubbles or the flow of liquid.
You can see this method in the video below
Non-destructive testing
You can find more information on our dedicated page