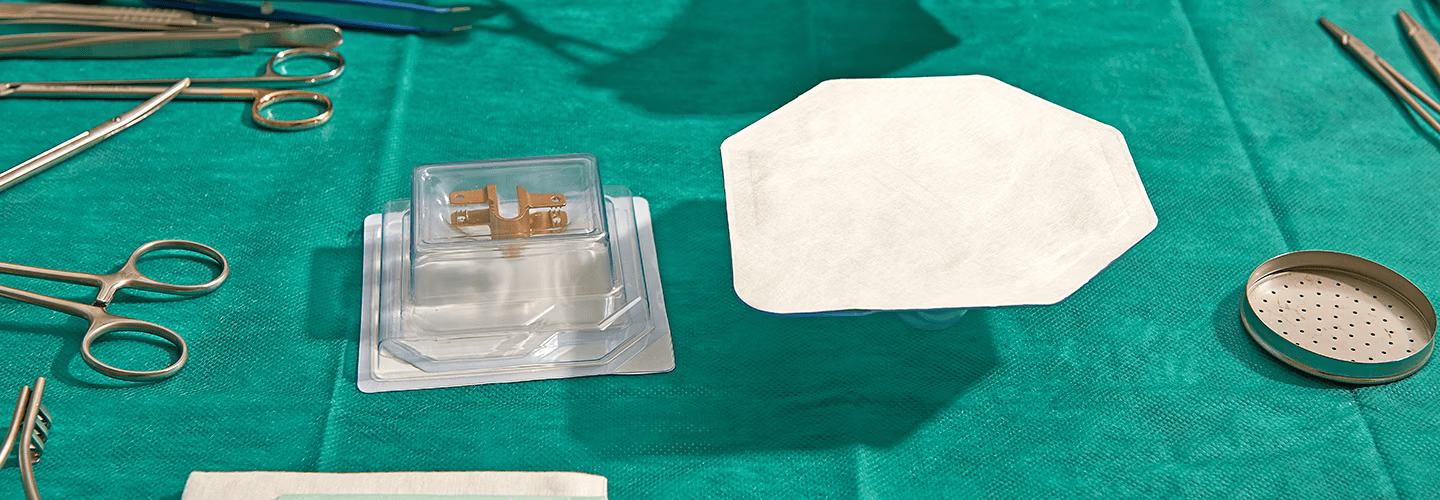
We hear a lot of praise for Tyvek®, the non-woven material patented by DuPont de Nemours. It was invented over 50 years ago in 1967. Appreciated for its many properties, it is used in the manufacture of many of our customers’ packaging. To guarantee the integrity of their packaging, we carry out leak tests adapted to this specific material. Our vacuum chambers can be adapted to several leak detection methods for porous materials such as Tyvek®.
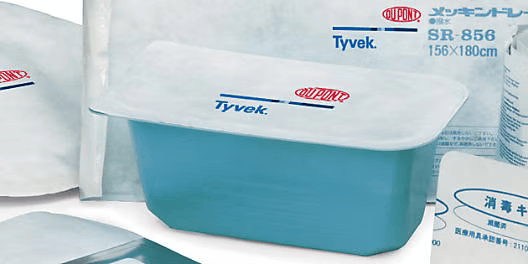
What is Tyvek® ?
A quick introduction to Tyvek®
Developed and marketed by DuPont for many years, Tyvek® is a synthetic non-woven material made from 100% high-density polyethylene (HDPE) fibres.
To the eye and to the touch, Tyvek® looks like paper, but offers far superior properties. Lightweight and durable, this porous material is breathable while remaining resistant to water, abrasion, bacterial penetration and ageing.
These remarkable properties make it ideal for a wide range of applications. Tyvek® can be used to close rigid packaging or to make complete Tyvek®-based ‘bags’. It is used in particular in medical and pharmaceutical packaging.
Tyvek® comes in the form of paper (rigid structure) or textile (flexible structure). It is available in sheets or rolls of various sizes.
Tyvek® properties
Tyvek® has unique properties that set it apart from other materials:
- Lightweight: with a density of 0.38 g/cm³, it has an exceptional strength-to-weight ratio.
- Tear and puncture resistance: Tyvek® non-woven fibres are randomly arranged and compressed to form a material with greater strength and elasticity than paper.
- Waterproofing and breathability: it prevents liquids from penetrating while allowing water vapour to pass through. This property makes it highly breathable.
- High chemical resistance: resistant to water, most solvents, acids and other chemicals.
- Low linting: lint-free and smooth on the surface, it ensures cleanliness in controlled environments.
- Printability: naturally opaque white, it can be printed using most traditional and digital printing techniques (offset, UV offset, flexography, screen printing, inkjet, etc.).
- Adaptability: it can be folded, glued, laminated, sewn, stapled and fixed. And repeatedly!
- Recyclable: non-toxic, Tyvek® can be 100% recycled, contributing to the environmental sustainability of products.
Examples of Tyvek® applications in sealed packaging
Combining the performance of paper, film and fabric, Tyvek® lends itself to a wide variety of applications.
It is used in watertight packaging thanks to its unique properties:
- Medical packaging: used for sterile packaging of medical devices, Tyvek® provides a barrier against micro-organisms and can be sterilised by various processes. In particular, it can be used to package products to be sterilised by oven drying.
- Protective envelopes and covers: manufacturers have adopted Tyvek® to make tear-resistant and water-resistant envelopes. These properties protect the product throughout the supply chain.
- Industrial packaging: manufacturers use it for packaging industrial products requiring protection against moisture and contaminants.
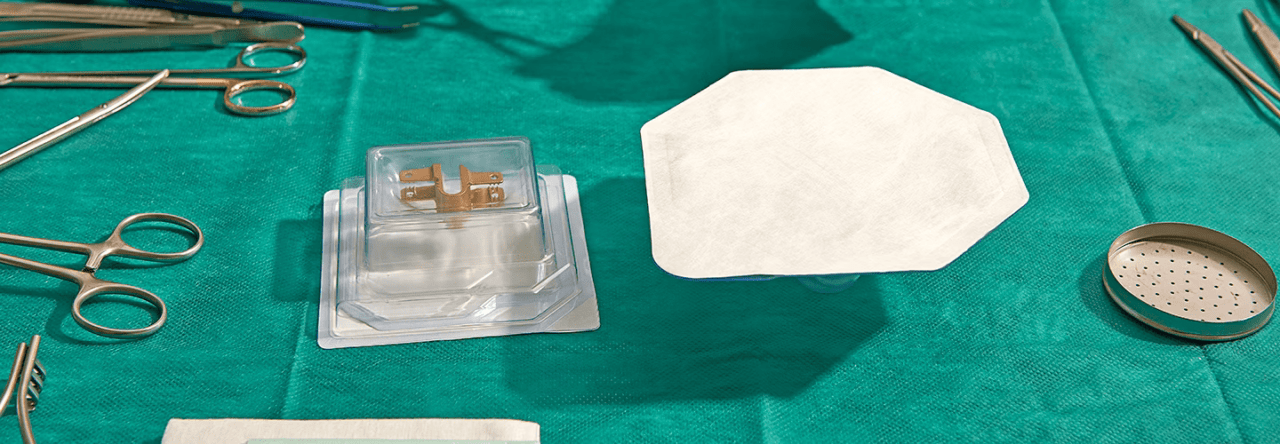
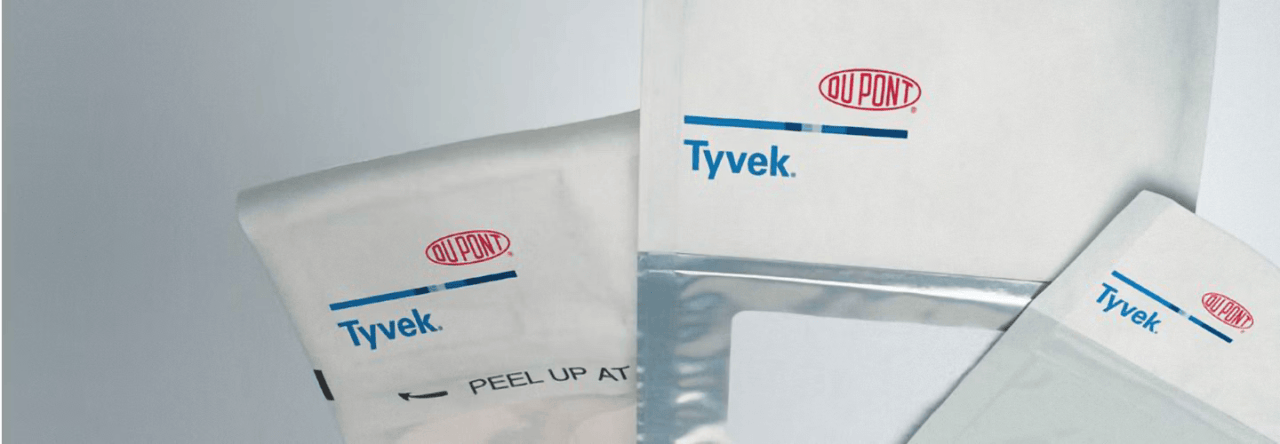
Recommended leak test methods for Tyvek®.
Use of a blocking agent for TYVEK® airtightness.
Tyvek® is naturally waterproof, but not airproof. To carry out our immersion tests, Tyvek® must be waterproofed using a blocking agent. This blocking agent, usually liquid polymers or film coatings, clogs the pores of the Tyvek®, preventing air from passing through.
Once the blocking agent has been applied, it must be allowed to dry as much as possible to ensure optimum effectiveness. We recommend a drying time of around 10 minutes.
Conventional "bubble test" (ASTM D3078) with TYVEK® waterproofed
Simple and intuitive, the bubble test or ASTM D3078 is the most widely used test for checking the tightness of flexible packaging, and is perfectly suited to testing Tyvek® and the integrity of seals. It can be used to detect major leaks in flexible packaging containing a head gas by the emission of bubbles.
Please note: a quantity of air in the headspace of the packaging is required to perform the classic bubble emission test. Without this residual air, the test cannot work. For under-vacuum packaging, we use an internal pressurisation test technique.
This leak detection method is also known as the ‘water bath’ or ‘immersion’ test. You’ll understand why when you learn about this process.
Here’s how to perform the bubble test:
- Immersion: the packaging sample is immersed in a vacuum chamber.
- Application of the pressure difference: the vacuum regulator built into the box is used to create the vacuum. A physical phenomenon occurs: the air trapped in the headspace of the pack tends to expand. As it increases in volume, it exerts pressure on the various sealing points in the pack (sealing, heat-sealing, stopper, etc.).
- Observation: the formation of air bubbles in any area of the tested packaging indicates a leak. Conversely, the absence of bubbles confirms that the packaging is airtight.
This technique not only detects the presence of one or more leaks, but also enables the precise location of the leak to be determined.
Depending on the size of the leak and the volume of air contained in the packaging, the flow of bubbles may stop after a certain length of time. You need to be quick to observe the bubbles.
Dye penetration test (ASTM F1929)
Some packages are too small for the bubble detection test. The volume of air inside the pack makes it difficult to detect the bubbles, which are too small and too few in number to be detected by the naked eye. In this case, a dye penetration test can be used (the most common dye is methylene blue). This standard test method allows visual detection of any channels or leaks in the sealing of Tyvek® packaging. The process is simple and easy to perform:
- Waterproofing: the surface of the packaging containing Tyvek® is waterproofed using the blocking agent.
- Immersion in a dye: the packaging is immersed in a bath of bright dye with high colouring power, such as methylene blue.
- Depressurisation: the chamber is depressurised and the vacuum maintained for approximately 10 minutes. The difference in pressure forces the air contained in the packaging to escape through any leaks.
- Return to atmospheric pressure: atmospheric pressure is then gradually restored in the chamber. This return to normal causes the volume of residual air in the packaging to contract. By suction, the coloured liquid penetrates through the leaks.
- Penetration time: it is important to allow sufficient observation time after this phase. Penetration of the dye can be slow, depending on the characteristics of the packaging and the size of the leaks. We observe a minimum period of 30 minutes to allow accurate detection of potential leaks.
- Observation of results: the outside of the pack is wiped clean and rinsed to remove any traces of dye. The inside of the pack is then examined. The presence of traces of dye on the inside indicates a leak in the seal, confirming the existence of a leak.
Internal pressure test (ASTM F2096)
The packaging may not contain enough air to perform these standard tests. ASTM F2096 can be used. This method involves detecting large leaks in packaging by internal pressurisation. It has been validated for non-porous and non-woven materials such as Tyvek®.
The process is as follows:
- Waterproofing: using the blocking agent, we waterproof the Tyvek® surface of our packaging.
- Immersion in a liquid developer: the sample is immersed in a water bath or a suitable solution.
- Applying internal air pressure: the packaging is pressurised with compressed air. For this stage, we use a needle and specialised patches which are glued to the packaging. The needle allows the patch to pass through the packaging without leaking around the needle. The patch acts as a watertight buffer zone. The standard tells us that you need to inject between 0 and 50 mbar of pressure in addition to atmospheric pressure.
- Observation of bubbles: the appearance of bubbles on the surface of the packaging indicates the presence of leaks. The size, frequency and location of the bubbles can be analysed to determine the extent and nature of any leaks.
Unlike the vacuum testing technique, the flow of bubbles is regular and cannot be stopped by pressure equalisation.
These tests are effective methods for assessing the integrity of packaging containing Tyvek®. CONTROL SENSEI uses these different methods for the quality control of packaging for all sectors of activity: agri-food, pharmaceutical and for packaging designed to provide a contamination-free environment for the product. These methods guarantee consumer safety and compliance with safety standards.
These so-called ‘destructive’ tests can damage the packaging and its container. CONTROL SENSEI can also offer non-destructive technologies.
Advantages of vacuum chambers for leak-testing Tyvek®.
Vacuum chambers offer a number of advantages for testing the watertightness of Tyvek® :
- Ease of use: these sealing boxes are intuitive and easy to use. They make testing a breeze.
- Wide range of applications: versatile and adaptable, the housings enable leak testing for a wide range of applications. These range from packaging integrity testing to the testing of pharmaceutical and medical products.
- Reproducibility of results: vacuum chambers enable a test to be repeated with the same vacuum level and the same test parameters. They guarantee comparable results from one test to the next and from one operator to the next.
- Machine customisation: vacuum chambers can be customised to meet the specific needs of manufacturers. Chamber size, negative air pressure range, leak detection options… So many options for assessing the quality and consistency of your packaging materials.