Inficon Contura S400 et Inficon Contura S600
Leak testing of food and pharmaceutical packaging.
The innovative Contura S400 leak detector offers packaging machine manufacturers, the food industry and the pharmaceutical industry in general a unique solution for inspecting the sealing of capsules, Modified Atmosphere Packaging (MAP) and other types of packaging, in accordance with DIN EN 1779 and closely aligned with ASTM F2338-09. Unlike other solutions, it can detect coarse leaks as well as fine leaks that are undetectable to the naked eye or by the immersion test method (also known as the “bubble test”). Contura S400’s unique technology can detect any leak (not just damage to seals) without the use of tracer gas and without damaging or soiling the packaging.
This non-destructive technology will save you money and ensure that your tested products are no longer scrapped.

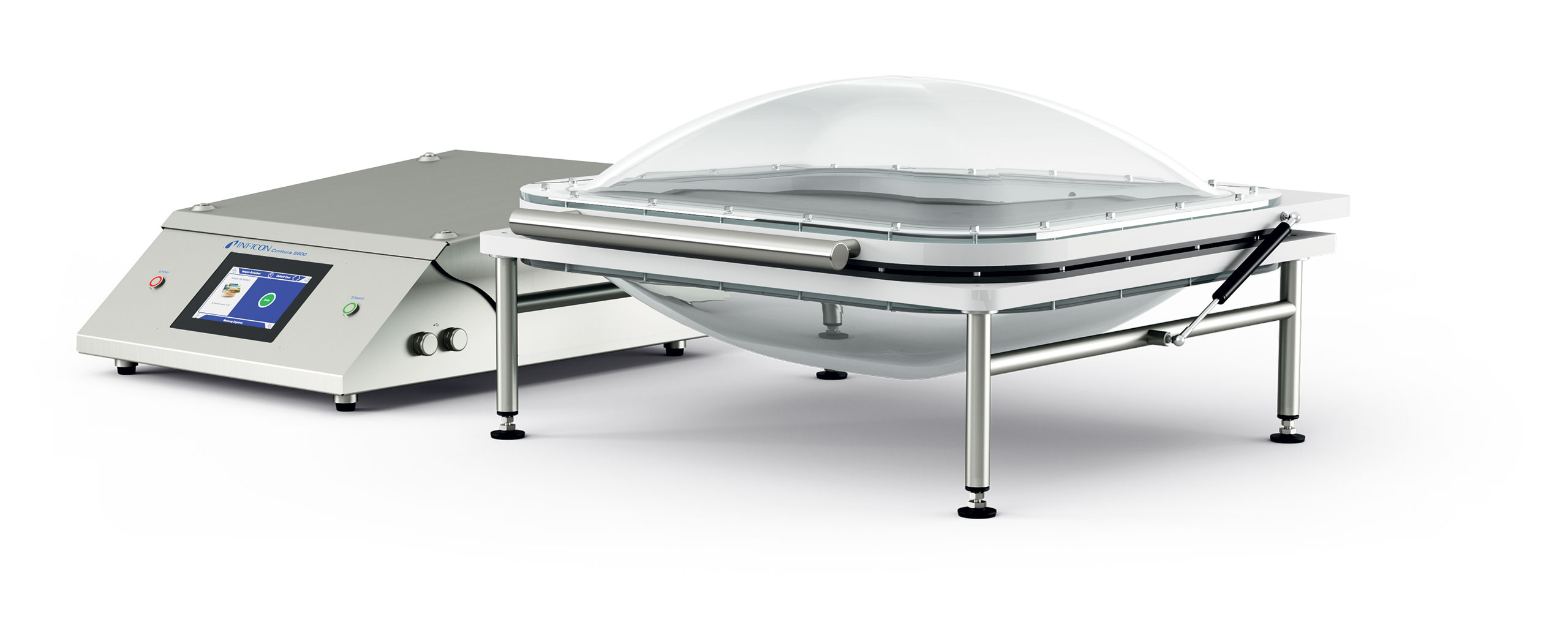
Technical specifications
Modèle Contura S400 | Modèle Contura S600 | |
Device material | Acier inoxydable, IP 20D | Acier inoxydable, IP 20D |
Device calibration | Avec le kit Inficon | Avec le kit Inficon |
Appliance dimensions | 725 x 535 x 475 mm | 800 x 780 x 420 mm |
Useful dimensions for testing | 400 x 350 x 200 mm | 550 x 450 x 250 mm |
Display | écran tactile 7 pouces | écran tactile 7 pouces |
Electric supply | 115/230 V ±10% 50 / 60 Hz |
115/230 V ±10% 50 / 60 Hz |
Interfaces | USB / LAN / RS232 | USB / LAN / RS232 |
Minimum detected leak size | inférieure à 10 µm | 10 µm |
Test duration | inférieur à 12 secondes | inférieur à 12 secondes |
Switch-on time | inférieur à 1 min | inférieur à 1 min |
Overall weight | 46kg | 61kg |
Packaging integrity in accordance with DIN EN 1779
This joint tester is also simple and accurate to use. The flexible test chamber is made up of two highly elastic membranes. By creating a vacuum, these membranes hermetically seal the packaging under test. The leak detector analyses the increase in pressure in a matter of seconds. The Contura S400 seal tester can therefore detect even the smallest leaks quickly and reliably.
If you are interested in this product and would like an on-site demonstration, please contact us.
Non-destructive testing (NDT) plays a crucial role in quality control. They offer many advantages over traditional testing methods, which often require the destruction or alteration of a sample. Here’s why NDT is so beneficial:
Firstly, non-destructive testing allows materials and products to be inspected without damaging them. This means that samples can be reused or marketed without damage, reducing production costs.
In addition, NDT offers high accuracy in detecting defects. In our case, a differential pressure sensor is used. Its accuracy allows it to address leaks of less than 10µm. This ensures the quality of finished products and avoids potential problems.
Non-destructive testing is also fast and efficient. They enable large quantities of materials or products to be inspected in a short space of time, speeding up the quality control process and reducing production lead times.
Last but not least, NDT helps to improve operational safety. They can detect structural defects or hidden faults that could compromise product reliability or safety.
In short, non-destructive testing offers an efficient, accurate and cost-effective way of checking the quality of materials and products without damaging them. Their use helps to guarantee high quality standards, reduce production costs and improve safety.
Eliminating the need to throw away samples also helps preserve our planet, and at Control Sensei, preserving the environment is one of our core values.